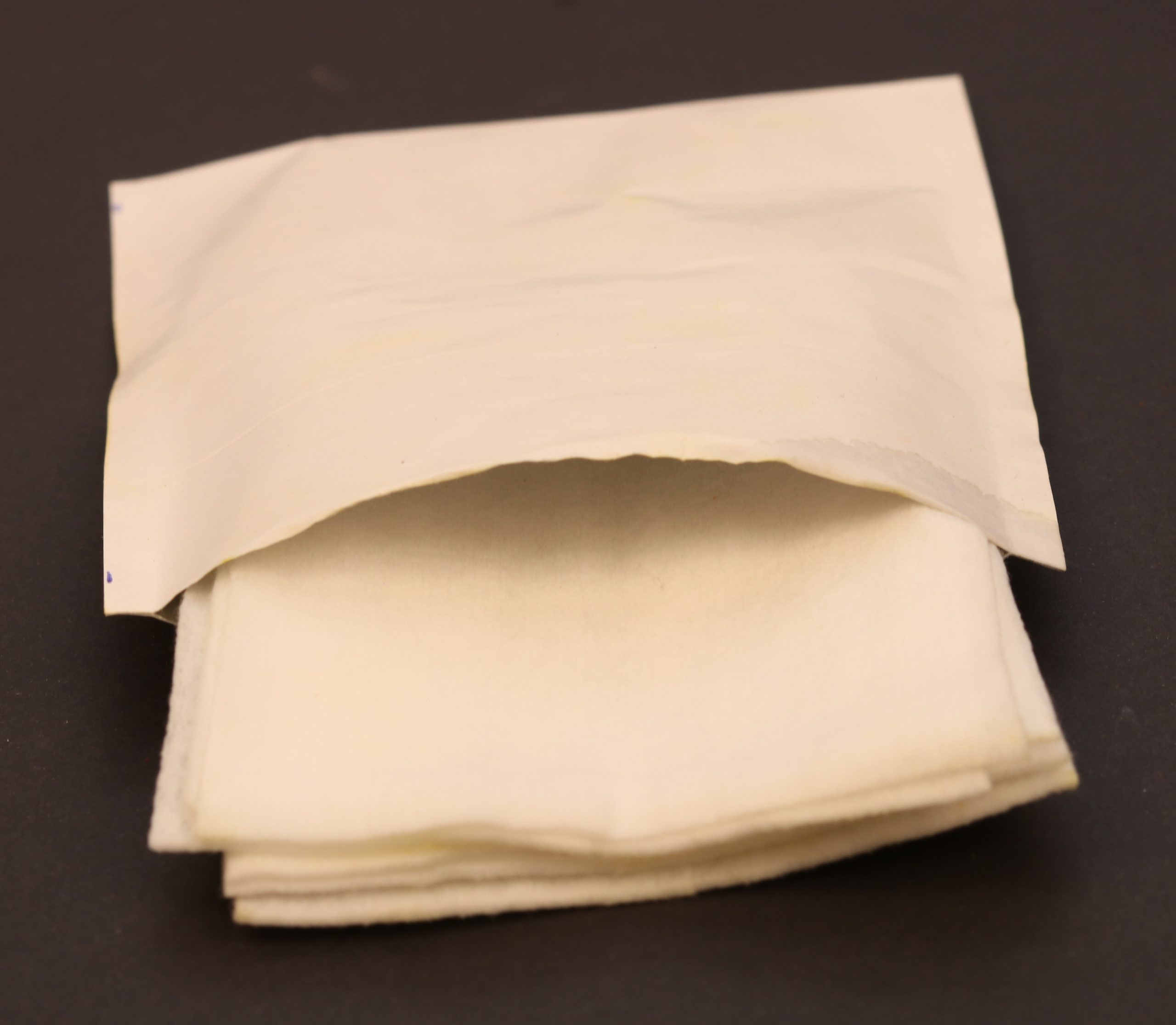
Heat Sealable Paper Foil Laminate: A Comprehensive Guide
Heat sealable paper foil laminate, commonly known as HS laminates, is a popular packaging material used in a wide range of industries. It is a multi-layered composite material that combines the benefits of different materials to provide exceptional strength, durability, and barrier properties.
Understanding Heat Sealable Paper Foil Laminates
In this section, we’ll take a deep dive into what heat sealable paper foil laminates are, their components, types, advantages, manufacturing process, and applications.
What is Heat Sealable Paper Foil Laminate?
Heat sealable paper foil laminate is a multi-layer material consisting of a paper layer, a thin layer of aluminum foil, and a layer of the polymer film. The layers are bonded together using a heat-sealing process to form a single, flexible sheet with excellent barrier properties.
Heat sealable paper foil laminates are widely used in the food packaging industry due to their excellent barrier properties. They protect the packaged product from moisture, oxygen, light, and other environmental factors that can cause spoilage, contamination, and loss of quality. They are also used in the medical and pharmaceutical industries to package sensitive products that require protection from external factors.
Components of Heat Sealable Paper Foil Laminate
HS laminates typically consist of three or more layers, each playing a specific role in its overall performance. The three primary layers are:
- Paper Layer: The paper layer adds strength and rigidity to the laminate and provides a printable surface for branding and other information. It is usually made of kraft paper or bleached paperboard, depending on the application.
- Aluminum Foil Layer: The aluminum foil layer provides a barrier against water vapor, oxygen, light, and other environmental factors that can damage the packaged product. It is usually 7-9 microns thick and is laminated to the paper layer using a heat-sealing adhesive.
- Polymer Film Layer: The polymer film layer adds another level of barrier protection and ensures that the laminate can withstand the rigors of packaging and transportation. It is usually made of polyethylene or polypropylene and is laminated to the aluminum foil layer using a heat-sealing adhesive.
Related Topic: Eco-Friendly Packaging Made Easy: How Biodegradable Paper is Revolutionizing the Industry
Types of Heat Sealable Paper Foil Laminates
HS laminates come in various types, each designed for specific packaging applications. Some of the common types include:
- Two-layer HS laminates: These are the most basic types of HS laminates, consisting of a paper layer and an aluminum foil layer. They are suitable for use in packaging dry goods such as snacks, coffee, and tea.
- Three-layer HS laminates: These laminates add an additional layer of polymer film for added strength and durability. They are ideal for packaging products that are prone to puncture and abrasion, such as pet food, detergents, and chemicals.
- Four-layer HS laminates: These laminates feature an additional barrier layer between the aluminum foil and polymer film layer for increased moisture and oxygen barrier protection. They are ideal for packaging perishable goods such as meat, cheese, and baked goods.
The choice of HS laminate depends on the specific packaging requirements of the product. For example, products that require high barrier protection against moisture and oxygen, such as meat and cheese, would require a four-layer HS laminate. On the other hand, products that require minimal barrier protection, such as dry goods, would require a two-layer HS laminate.
Advantages of Heat Sealable Paper Foil Laminates
HS laminates offer several advantages over other packaging materials, including:
- Excellent barrier properties: HS laminates provide a high level of protection against moisture, oxygen, light, and other environmental factors that can damage the packaged product.
- Customizable: HS laminates can be customized to meet specific packaging requirements, such as size, shape, and barrier properties.
- Printable: The paper layer of HS laminates provides a printable surface for branding and other information, making it an ideal packaging material for marketing and promotional purposes.
- Cost-effective: HS laminates are a cost-effective packaging solution for a wide range of products.
Manufacturing Process of Heat Sealable Paper Foil Laminates
The manufacturing process of HS laminates involves several steps, including:
- Printing: The paper layer is printed with the required design and information, such as branding and product details.
- Lamination: The aluminum foil layer and polymer film layer are laminated to the paper layer using a heat-sealing adhesive. The laminated sheet is then cooled and rolled into a large roll.
- Slitting: The large roll is slit into smaller rolls of the required width and length, depending on the specific packaging requirements of the product.
- Conversion: The smaller rolls are converted into the final packaging form, such as bags, pouches, or wraps, using various conversion processes, such as cutting, sealing, and filling.
Applications of Heat Sealable Paper Foil Laminates
HS laminates are widely used in various industries for packaging a wide range of products, including:
- Food: HS laminates are used to package a wide range of food products, including snacks, coffee, tea, pet food, and perishable goods such as meat, cheese, and baked goods.
- Medical and pharmaceutical: HS laminates are used to package sensitive medical and pharmaceutical products that require protection from external factors such as moisture, oxygen, and light.
- Industrial: HS laminates are used to package industrial products such as detergents, chemicals, and lubricants.
Overall, heat sealable paper foil laminates offer a versatile and cost-effective packaging solution for a wide range of products, providing excellent barrier properties, customizability, and printability.
Advantages of Using Heat Sealable Paper Foil Laminates
Heat sealable paper foil laminates have become a popular choice among manufacturers and consumers alike due to their numerous advantages. These laminates offer a range of benefits, including:
Barrier Properties
HS laminates provide excellent barrier properties against moisture, oxygen, light, and other environmental factors that can damage the packaged product.
This helps to maintain the product’s freshness and quality for an extended period. The barrier properties of HS laminates also make them suitable for packaging products that require protection from external factors, such as food, pharmaceuticals, and cosmetics.
Seal Strength and Integrity
HS laminates provide a strong, airtight seal that prevents air and moisture from entering the package, keeping the product fresh for longer. The seal strength and integrity also protect against contamination, tampering, and other hazards during transportation and storage. This makes HS laminates an ideal choice for products that require a secure and safe packaging solution, such as medical devices and sensitive electronics.
Sustainability and Eco-friendliness
HS laminates are more eco-friendly than most traditional packaging materials due to their biodegradability and recyclability. They are made from renewable resources, such as paper and foil, which can be easily recycled or composted.
Additionally, they use fewer resources in production, lowering their environmental footprint. The sustainability and eco-friendliness of HS laminates make them an ideal choice for companies that prioritize environmental responsibility and want to reduce their carbon footprint.
Versatility in Packaging Applications
HS laminates are suitable for use in a wide range of packaging applications, including food, pharmaceutical, cosmetic, and industrial packaging. They can be tailored to specific needs, such as barrier requirements and branding, making them a popular choice among manufacturers and consumers alike. HS laminates are also available in a variety of sizes and shapes, making them suitable for packaging products of different shapes and sizes.
In conclusion, heat sealable paper foil laminates offer numerous advantages over traditional packaging materials. They provide excellent barrier properties, seal strength and integrity, sustainability, and versatility in packaging applications. These benefits make HS laminates an ideal choice for companies that want to ensure the quality and safety of their products while also prioritizing environmental responsibility.
Manufacturing Process of Heat Sealable Paper Foil Laminates
The manufacturing process of HS laminates involves several stages, including raw material selection, lamination process, quality control, and testing. However, the process is not as simple as it sounds. It requires a lot of precision, expertise, and attention to detail to produce high-quality HS laminates.
Raw Material Selection
The raw materials used in HS laminates must be carefully selected to ensure the desired properties and performance. The paper used in the laminate must be of high quality and should have a smooth surface to ensure good printability. The aluminum foil used in the laminate should be of the appropriate thickness and must have a consistent surface finish. The polymer film used in the laminate should be of high quality and must have good heat-sealing properties.
The selection of raw materials is critical to the performance of the final product. The wrong choice of materials can result in poor printability, weak seals, and compromised barrier properties.
Lamination Process
The lamination process involves bonding the layers together using heat and pressure. The layers are first coated with an adhesive and then passed through a series of rollers to bond them together.
The temperature and pressure used in the lamination process must be carefully controlled to ensure that the layers are bonded together properly. The adhesive used in the lamination process must be of high quality and should be able to withstand the heat and pressure of the lamination process.
The lamination process is critical to the performance of the final product. Poor lamination can result in weak seals, delamination, and compromised barrier properties.
Quality Control and Testing
HS laminates undergo rigorous quality control and testing to ensure that they meet the required standards for strength, durability, and barrier properties. This may involve testing for seal strength, puncture resistance, and other parameters. The laminates are also tested for their ability to withstand various environmental conditions such as temperature, humidity, and light exposure.
The quality control and testing process is critical to ensuring that the final product meets the required standards. Any defects in the laminates can result in product failure, which can be costly for the manufacturer and the end user.
In conclusion, the manufacturing process of HS laminates is a complex and precise process that requires a lot of expertise and attention to detail.
The selection of raw materials, the lamination process, and quality control and testing are critical to the performance of the final product. By following these processes, manufacturers can produce high-quality HS laminates that meet the required standards for strength, durability, and barrier properties.
Applications of Heat Sealable Paper Foil Laminates
HS laminates are versatile and can be used in various packaging applications, including:
Food Packaging
HS laminates are ideal for packaging food products such as snacks, cereals, frozen foods, and baked goods. They provide excellent barrier properties, seal strength, and durability, keeping the food fresh and protected.
Pharmaceutical Packaging
HS laminates are widely used in pharmaceutical packaging due to their exceptional barrier properties and versatility. They are ideal for packaging tablets, capsules, and other medicinal products that require protection against moisture, oxygen, light, and other environmental factors.
Cosmetic Packaging
HS laminates are commonly used in cosmetic packaging due to their excellent printing properties and versatility. They provide an attractive, moisture-proof, and airtight package that protects the product from environmental factors and extends its shelf-life.
Industrial Packaging
HS laminates are used in various industrial packaging applications, including packaging for chemicals, textiles, and other industrial products. They provide the required barrier properties and durability to protect the products from damage during transportation and storage.
Conclusion
Heat sealable paper foil laminates are excellent packaging material that provides exceptional strength, durability, and barrier properties. They are used in various industries for packaging food, pharmaceuticals, cosmetics, and industrial products.
Understanding their components, types, advantages, manufacturing process, and applications can help manufacturers and consumers make informed decisions about their use.